[摘要]:本文作者綜述化工智能化生產(chǎn)技術(shù)及其在化學工業(yè)中的應(yīng)用與進展。內(nèi)容涉及位于化工企業(yè)智能化生產(chǎn)上層的ERP、SCM、E-Business和DSS,中層的EOM 和MES,下層的DCS、PLC和ESD等,同時指出化工控制技術(shù)的發(fā)展方向。
[關(guān)鍵詞]:化工 智能化生產(chǎn) SCM EOM MES
智能化生產(chǎn)技術(shù)是制造業(yè)不斷吸收機械、電氣、電子、信息(計算機、網(wǎng)絡(luò)、通信、控制論、人工智能等)、能源及現(xiàn)代系統(tǒng)管理等領(lǐng)域的成果,并將其綜合運用于產(chǎn)品研發(fā)、設(shè)計、制造、檢測、銷售、使用、服務(wù)乃至回收的全過程,以實現(xiàn)優(yōu)質(zhì)、高效、低耗、清潔、敏捷、柔性生產(chǎn),提高對市場動態(tài)多變的適應(yīng)能力和競爭能力的制造技術(shù)的總稱。
本文作者綜述化工智能化生產(chǎn)技術(shù)及其在化學工業(yè)中的應(yīng)用與進展。
1 儀表與自動化系統(tǒng)的數(shù)字化
儀表與自動化系統(tǒng)經(jīng)歷了氣動儀表(PCS,即第一代過程控制系統(tǒng))、基于電動儀表(0~10mA、4~20mA模擬電流信號)的電動單元組合式模擬儀表控制系統(tǒng)(ACS,即第二代過程控制系統(tǒng)" title="過程控制系統(tǒng)" target="_blank">過程控制系統(tǒng))、基于計算機的直接數(shù)字控制和監(jiān)督計算機控制或計算機控制系統(tǒng)(即DDC、SCC、CCS,第三代過程控制系統(tǒng))和基于微處理器的分布式控制系統(tǒng)(DCS,即第四代過程控制系統(tǒng))后,又發(fā)展到了第五代過程控制系統(tǒng)。
第四代DCS產(chǎn)品的主要標志是集成,其覆蓋現(xiàn)場儀表層、控制裝置單元層、工廠層和企業(yè)層4個層次。而前三代只覆蓋前三層,第四代則已成為過程控制和信息管理的綜合信息平臺。其功能包括過程控制、PLC、RTU(遠程采集發(fā)送器)、FCS、多回路調(diào)節(jié)器、智能采集和控制單元等功能集成以及組態(tài)軟件、I/O組件、PLC單元等產(chǎn)品集成,還包容過程控制、邏輯控制、批處理控制,并實現(xiàn)混合控制。
1980年后出現(xiàn)的基于現(xiàn)場總線技術(shù)(Fieldbus)的現(xiàn)場總線控制系統(tǒng)(FCS)即第五代過程控制系統(tǒng)。目前正在發(fā)展過程中,其標準尚未統(tǒng)一,總體上是DCS、PLC、FCS三者的結(jié)合。
今后的發(fā)展趨勢是發(fā)展智能儀表和現(xiàn)場總線技術(shù),自動化儀表與裝置正在跨入真正的數(shù)字化、網(wǎng)絡(luò)化和智能化時代。其技術(shù)發(fā)展的主流則是測量信息數(shù)字化、檢測儀表智能化和現(xiàn)場控制與過程管理一體化。21世紀頭10年的熱點是傳感、執(zhí)行與通信。儀器儀表不僅僅是工業(yè)時代的測量“工具”,而且是當今信息時代的信息源頭。近10年內(nèi),傳感器的數(shù)量將增加幾十倍,自動化系統(tǒng)中的非控制變量信息比例也將成倍增加,將利用固體物理特性產(chǎn)生的敏感機理開發(fā)成物理、化學、生物等敏感元件或傳感器,使傳感器技術(shù)向微型化、高精度、低能耗、智能化、集成化發(fā)展。信號無線傳輸、過程遠程無線監(jiān)控以及非接觸式控制器也是方向。微型傳感器和組分模型在分子級對物理化學過程進行跟蹤和控制,而且是從原料的進廠到產(chǎn)品的出廠確保實現(xiàn)潛在的最大價值。微型智能傳感器在線實時實現(xiàn)化驗分析。由于內(nèi)嵌智能傳感器,材料和設(shè)備也是智能的,可在線連續(xù)測量溫度、壓力、應(yīng)力、應(yīng)變、振動、位移等參數(shù),及時預(yù)測預(yù)報潛在的損壞部位,并有自診斷、自修復(fù)功能,在出現(xiàn)事故前維修完畢。
化工測量分析也將成為現(xiàn)場基礎(chǔ)技術(shù),成倍或幾十倍地提高測量分析的分辨率和靈敏度,分析周期將縮短到十至幾十分之一,普遍采用如核磁共振(NMR)、微波(Microware)、近紅外光譜(NIR)分析技術(shù),實現(xiàn)分子級的實時、在線、多指標、多功能、多用途的化驗分析。傳統(tǒng)的質(zhì)量化驗分析室將由實時、在線、連續(xù)的產(chǎn)品質(zhì)量、成分分析系統(tǒng)取代,最大限度地改善過程控制和環(huán)境監(jiān)測質(zhì)量。
動態(tài)的信息網(wǎng)絡(luò)將在石油化工廠運行。成千上萬的傳感器通過網(wǎng)絡(luò)直接、實時傳送全廠的數(shù)據(jù)和圖像信息,并為嚴格、實時的優(yōu)化模型提供數(shù)據(jù);還與組分模型結(jié)合,在分子級描述過程的變化,預(yù)測產(chǎn)品組成,實現(xiàn)全廠的實時連續(xù)優(yōu)化。先進控制將普及到全裝置、全廠范圍。依靠過程信息進行統(tǒng)計診斷、過程統(tǒng)計控制,將是高度自動化的關(guān)鍵。建立監(jiān)測數(shù)據(jù)庫,只有首次出現(xiàn)的事故,才需要專家處理。在線監(jiān)測可實現(xiàn)提前6個月的故障診斷和智能預(yù)報警。建立過程模型,進行靜態(tài)和動態(tài)模擬,模擬速度將比現(xiàn)在提高幾十倍或幾百倍,一天足以模擬全廠的所有裝置和單元。
PLC、SCADA、DCS 控制系統(tǒng)、現(xiàn)場總線、工業(yè)以太網(wǎng)的發(fā)展趨勢呈現(xiàn)以下特點:
(1)系統(tǒng)功能從低層(現(xiàn)場控制層)逐步向高層(監(jiān)督控制、生產(chǎn)調(diào)度管理)擴展。
(2)控制功能由單一的回路控制,逐步向綜合的邏輯控制、順序控制、程序控制、批量控制、配方控制、混合控制以及先進控制發(fā)展。
(3)系統(tǒng)構(gòu)成部件由DCS廠家專有的產(chǎn)品變?yōu)殚_放的市場采購產(chǎn)品。
(4)技術(shù)標準逐漸走向開放、統(tǒng)一、集成。
(5)由于開放性推進產(chǎn)品的趨同性,迫使DCS廠商向高層、與生產(chǎn)工藝結(jié)合緊密的高級控制功能發(fā)展,以求得短時間的差異性。
(6)數(shù)字化向現(xiàn)場儀表裝置延伸,導(dǎo)致DCS體系結(jié)構(gòu)和現(xiàn)場功能數(shù)字化、智能化、分散化。
(7)標準的串行總線(以太網(wǎng)及其之上的TCP/IP協(xié)議、Porfibus、Modbus等)已成為DCS等工業(yè)控制系統(tǒng)中車間一級控制器廣泛采用的標準通信網(wǎng)絡(luò)和協(xié)議,但不可能取代底層的現(xiàn)場總線。
(8)生產(chǎn)區(qū)域現(xiàn)場控制裝置與控制室內(nèi)的自動控制裝置之間的數(shù)字式、串行和多點通信的數(shù)據(jù)總線稱為現(xiàn)場總線(FieldBus)?,F(xiàn)場總線技術(shù)在20世紀70年代末出現(xiàn),90年代成為熱點,是從模擬儀表到數(shù)字計算機的現(xiàn)場信號傳輸標準,真正解決了從儀表到計算機的換代問題,促進了儀表信息處理的現(xiàn)場化,形成了全數(shù)字化(變量單元和執(zhí)行單元)、信息化和集成化的新一代DCS?,F(xiàn)場總線技術(shù)將使現(xiàn)在的模擬與數(shù)字混合的、分散控制系統(tǒng)(DCS)更新?lián)Q代為全數(shù)字式的徹底分散的現(xiàn)場總線控制系統(tǒng)(FCS),真正做到危險分散、控制分散、信息集中和監(jiān)控集中。
(9)新一代即第四代DCS有過程知識系統(tǒng)、工廠資源管理系統(tǒng),例如ABB的Industrial IT系統(tǒng)和HOLLiAS的國產(chǎn)HOLLiAS-Macs系統(tǒng)等,主要特征是集成和信息化,實現(xiàn)全廠實時控制以及PCS、MES和ERP 層的信息集成;混合控制系統(tǒng):包容PLC、RTU、FCS等,進一步分散化;I/O處理單元小型化、智能化、低成本;平臺(組態(tài)軟件平臺、人機界面平臺、現(xiàn)場控制組件、I/O組件等)開放與應(yīng)用專業(yè)化;提供了豐富的設(shè)備診斷、維修和管理功能。新一代DCS不僅是綜合控制系統(tǒng),而且是集成化的綜合控制與信息管理系統(tǒng)。
(10)PLC是一種產(chǎn)品形態(tài)的、可獨立運行的、執(zhí)行直接控制功能的控制器系統(tǒng)。早期以邏輯控制為主。其小型PLC的I/O總數(shù)較少,約數(shù)十點;中型則由主機架和擴展機架組成,I/O總數(shù)則達500點左右;大型PLC系統(tǒng)由多臺PLC和高速網(wǎng)絡(luò)構(gòu)成,可實現(xiàn)數(shù)千個I/O點的強大控制功能。PLC再與第三方人機界面和組態(tài)軟件配合,可組成完整的監(jiān)督控制系統(tǒng)。
另外,早期的SCADA系統(tǒng)只是針對遠程測量和監(jiān)控,近年來的SCADA 則基于廣域網(wǎng)和互聯(lián)網(wǎng),而且不局限于遠程遙測遙控,而泛指以監(jiān)督控制為主的各種計算機系統(tǒng),其組成可以是PLC設(shè)備,也可以是DCS,或者是專用的SCADA產(chǎn)品。
2 生產(chǎn)經(jīng)營管理與生產(chǎn)過程控制的集成化或一體化
MES屬于企業(yè)管理應(yīng)用軟件的范圍,起源于離散工業(yè),又擴展到流程工業(yè)。DCS普及后,至今DCS和MES之間的接口還是薄弱環(huán)節(jié)。所以,在MES中,專門設(shè)計了PIMS(工廠信息管理系統(tǒng)),接收DCS實時數(shù)據(jù),實現(xiàn)生產(chǎn)績效管理和運行數(shù)據(jù)的集成。
流程工業(yè)MES的主要功能模塊一般包括短期生產(chǎn)計劃、作業(yè)排產(chǎn)和調(diào)度(APS)、過程控制和管理、維護管理、技術(shù)信息管理、過程優(yōu)化控制(APC)、提高質(zhì)量管理功能的LIMS以及與ERP之間的連接。還有流程工業(yè)生產(chǎn)的特殊需求,如數(shù)據(jù)調(diào)理和校正、運行數(shù)據(jù)統(tǒng)計、公用工程平衡管理、設(shè)備壽命預(yù)測、設(shè)備性能計算、罐區(qū)管理、罐區(qū)平衡、物料平衡等,都作為MES的單一功能模塊,并往往集成到MES系統(tǒng)中。
下面列舉國外兩個針對流程工業(yè)尤其適用于石油化工的比較突出和優(yōu)秀的MES產(chǎn)品方案:
2.1 Honeywell的MES方案
Honeywell公司是世界著名的自動化儀表、過程控制和工業(yè)軟件公司,其MES產(chǎn)品從20世紀90年代末開始,先由單一的MES功能模塊發(fā)展到整體解決方案。
其MES產(chǎn)品的核心是Business.FLEX# PKS#。該產(chǎn)品將經(jīng)營目標轉(zhuǎn)化為生產(chǎn)操作目標,同時將經(jīng)過處理驗證的生產(chǎn)績效數(shù)據(jù)進行反饋,從而形成計劃管理層、生產(chǎn)執(zhí)行層和過程控制層三個層次的周期循環(huán)。
該產(chǎn)品由價值鏈管理(VCM)、先進計劃與調(diào)度(AP&S)、運行管理、油品調(diào)和及儲運自動化(BMA)和生產(chǎn)管理5個應(yīng)用套件共30多個模塊組成。價值鏈管理又包括銷售預(yù)測、運輸計劃、生產(chǎn)排產(chǎn)、原材料計劃、供應(yīng)鏈事件管理、庫存計劃、價值鏈循環(huán)優(yōu)化和生產(chǎn)計劃管理等。先進計劃調(diào)度包括原材料供應(yīng)及產(chǎn)品分配與優(yōu)化、原油組分分析、原油采購計劃、原油調(diào)度優(yōu)化、生產(chǎn)實況分析、油品調(diào)和調(diào)度等。運行管理包括操作指令下達、運行監(jiān)控、事件監(jiān)控、實驗室信息管理與集成、油罐組分跟蹤、產(chǎn)品規(guī)格管理、多單元生產(chǎn)運行計劃等。油品儲運及調(diào)和自動化包括調(diào)和調(diào)度計劃、在線調(diào)和優(yōu)化、調(diào)和比率控制和調(diào)和績效統(tǒng)計、油品輸轉(zhuǎn)及庫存跟蹤、罐存計量管理、輸轉(zhuǎn)模型建立、油品輸轉(zhuǎn)控制、油品移動路徑選擇等。生產(chǎn)管理包括物料平衡和庫存盤點、成本核算、組分計算與平衡、批量跟蹤與控制、原材料消耗統(tǒng)計、物料移動跟蹤、多單元生產(chǎn)運行計劃、操作指令下達和實驗室信息管理等。方案如圖1所示。
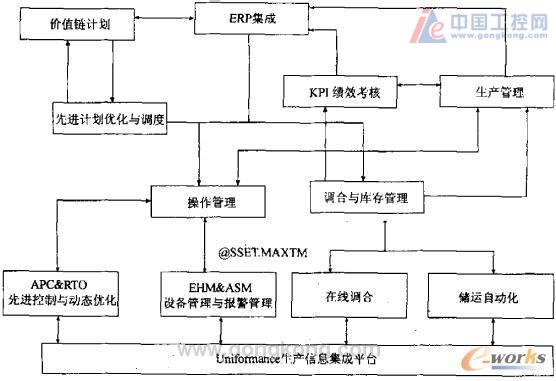
圖1 HoneywellMES解決方案
另外,Honeywell又將其MES解決方案與資產(chǎn)管理解決方案——@SSET.MAXTM、先進控制與區(qū)域優(yōu)化解決方案——Profit.PlusTM、生產(chǎn)信息集成平臺——Uniformance#等應(yīng)用套件和信息集成平臺整合為協(xié)同生產(chǎn)管理解決方案,也可看成是其廣義的MES或者是MES功能模塊的擴充。
2.2 ASPENTech的MES方案
美國ASPENTech公司是化學工業(yè)領(lǐng)域著名的流程模擬、先進控制和供應(yīng)鏈管理優(yōu)化軟件公司,近幾年經(jīng)過并購和整合,也定位在MES解決方案供應(yīng)商。它提出了企業(yè)運營管理的理念并開發(fā)集成了相應(yīng)的軟件產(chǎn)品。根據(jù)ASPEN的定義,企業(yè)運營管理(EOM)是一個企業(yè)級的集成解決方案,把ERP層、MES層和DCS層進行整合,高效地設(shè)計、管理和運營制造與供應(yīng)鏈的相關(guān)業(yè)務(wù)。根據(jù)ASPEN的觀點,ERP的功能是回答已發(fā)生了什么?而EOM的功能則是回答未來應(yīng)該怎么做并執(zhí)行這些決策。ASPEN公司用于過程工業(yè)運營管理的MES產(chǎn)品為ASPENPlantelligence,即智能工廠解決方案,如圖2所示。
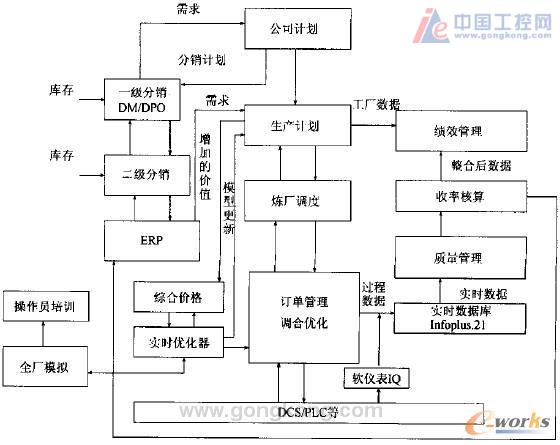
圖2 ASPENPlantelligence方案
該方案自1998年推出,并不斷發(fā)展和完善,得到了許多大型石油化工公司的采用。方案主要包括流程模擬、虛擬工廠模擬器、生產(chǎn)計劃與優(yōu)化、生產(chǎn)調(diào)度與優(yōu)化、先進控制與實時優(yōu)化(RTOPT)、實時數(shù)據(jù)庫與信息管理、數(shù)據(jù)校正與物料平衡、績效監(jiān)控與績效管理、油品調(diào)和、生產(chǎn)指令管理與操作日志、油品移動和罐區(qū)管理等11個功能模塊以及ASPENEnterprisePlatform(AEP)集成平臺,實現(xiàn)生產(chǎn)經(jīng)營管理與生產(chǎn)過程控制的一體化。
今后的發(fā)展趨勢是,生產(chǎn)執(zhí)行系統(tǒng)將走向成熟并成為應(yīng)用熱點,是解決過程控制層和經(jīng)營層之間信息隔斷的關(guān)鍵。據(jù)美國ARC公司調(diào)查,53%的客戶反映ERP對工廠生產(chǎn)存在著負面影響。其主要原因之一就是缺乏真實的、及時的、全面的生產(chǎn)過程現(xiàn)場信息,連接現(xiàn)場被忽略
,這就是生產(chǎn)執(zhí)行系統(tǒng)產(chǎn)生的原由。生產(chǎn)執(zhí)行系統(tǒng)將逐漸成為集成化的生產(chǎn)執(zhí)行系統(tǒng)(I-MES)。全面覆蓋生產(chǎn)計劃優(yōu)化、滾動調(diào)度、實時數(shù)據(jù)庫、數(shù)據(jù)校正、收率計算、成本控制、生產(chǎn)統(tǒng)計、KPI指標實時監(jiān)控、績效分析、流程模擬、質(zhì)量控制、在線優(yōu)化、先進控制、資產(chǎn)管理、設(shè)備診斷維護、罐區(qū)計量輸轉(zhuǎn)、庫存管理自動化、在線優(yōu)化控制、質(zhì)量控制、比率控制。并且下聯(lián)DCS、PLC、ESD(緊急停車系統(tǒng))和ASM(異常事件管理系統(tǒng)),上聯(lián)ERP、SCM、HSE、E-Business、E-Cooperation和DSS(決策支持系統(tǒng))。過去的10年,MES理念、技術(shù)和軟件產(chǎn)品已經(jīng)成熟,今后10~20年,將是在石油化工中迅速普及的技術(shù)領(lǐng)域。
3 企業(yè)內(nèi)部與外部供應(yīng)鏈管理一體化
ERP是對企業(yè)資源進行有效綜合的計劃與管理,是提高企業(yè)經(jīng)營效率和效益的手段和概念。其中心是計劃,而不是財務(wù)。實現(xiàn)這個目的軟件叫ERP軟件,當前德國SAP公司的R/3最有名。ERP面向企業(yè)的主要業(yè)務(wù),包括產(chǎn)品定貨、原材料采購、生產(chǎn)制造、配送、銷售、會計等一系列業(yè)務(wù)流,是覆蓋全公司的信息系統(tǒng),其關(guān)鍵業(yè)務(wù)包括計劃、財務(wù)會計和管理會計,還有人力資源管理等。ERP的數(shù)據(jù)庫要與實時數(shù)據(jù)庫相連,提取生產(chǎn)過程的有關(guān)數(shù)據(jù),ERP又和供應(yīng)鏈管理(SCM)集成。
供應(yīng)鏈指相互之間提供原材料、零部件、產(chǎn)品、技術(shù)或者服務(wù)的生產(chǎn)商、供應(yīng)商、零售商以及合作伙伴等組成的網(wǎng)絡(luò)關(guān)系。供應(yīng)鏈管理(SCM)則是對供應(yīng)鏈中涉及的物流、資金流、信息流進行規(guī)劃、設(shè)計、管理與控制,從而提高供應(yīng)鏈中各個成員的效率、效益和競爭能力。最終保證客戶滿意,即在正確的時間把正確的產(chǎn)品或服務(wù)送到正確的地點。它是在企業(yè)資源計劃(ERP)的基礎(chǔ)上,把企業(yè)的生產(chǎn)過程、庫存系統(tǒng)、銷售系統(tǒng)與供應(yīng)商、零售商以及各種合作伙伴集成為一個有機體,最大限度地縮短工作周期,提高工作效率,有效利用資源,創(chuàng)造更大價值。
供應(yīng)鏈是將企業(yè)活動當作一種供需過程描述,即從最初獲取原材料到通過生產(chǎn)制造,轉(zhuǎn)換成最終產(chǎn)品,交付給最終用戶的采購、生產(chǎn)、銷售的若干供需環(huán)節(jié)的有序鏈接。供應(yīng)鏈管理是對供應(yīng)鏈所涉及的組織的集成和對物流、資金流、信息流的協(xié)同,提高供應(yīng)鏈相關(guān)企業(yè)的競爭能力??傊?yīng)鏈管理就是優(yōu)化和改進供應(yīng)鏈的所有活動。
廣義供應(yīng)鏈管理,包括供應(yīng)鏈規(guī)劃(SCP)、供應(yīng)鏈執(zhí)行(SCE)和傳統(tǒng)的進、銷、存管理;狹義供應(yīng)鏈管理,包括供應(yīng)鏈執(zhí)行和傳統(tǒng)的進、銷、存管理。供應(yīng)鏈管理與另外幾個概念有關(guān),但有區(qū)別,如圖3所示。
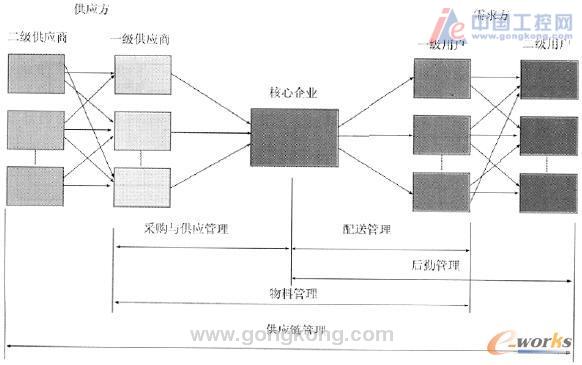
圖3 供應(yīng)鏈及其相關(guān)概念的關(guān)系
后勤管理是指經(jīng)過分銷渠道達到最終用戶的物料管理和信息管理,又發(fā)展為后勤工程、后勤管理和后勤分配。
物資配送管理,指處理與企業(yè)最直接的一級用戶之間的物流業(yè)務(wù),把產(chǎn)品銷售給用戶。最近幾年,后勤管理基本上泛指物流管理。
物料管理指供應(yīng)鏈中間部分的物流和信息流。即采購、庫存管理、倉儲管理、生產(chǎn)作業(yè)計劃控制、分銷配送管理等,包括從原料的采購進廠、入庫、生產(chǎn)再到產(chǎn)品交付給一級用戶。
供應(yīng)鏈管理的內(nèi)容從20世紀中期開始出現(xiàn)。對制造業(yè),從早期的MRP$到ERP就是它的起源。由MRP和MRP$到SCM,從企業(yè)內(nèi)部延伸到外部,都體現(xiàn)了供應(yīng)鏈管理的產(chǎn)生和發(fā)展進程。它在ERP的基礎(chǔ)上,把企業(yè)內(nèi)部經(jīng)營過程的所有業(yè)務(wù)系統(tǒng)如訂單、采購、庫存、計劃、生產(chǎn)、質(zhì)量、運輸、市場、銷售、服務(wù)等以及財務(wù)、人事管理均納入一條供應(yīng)鏈進行統(tǒng)籌管理。
20世紀80年代后期,一些重要的公司如BASF、DOW、Dupont發(fā)現(xiàn),單靠企業(yè)自身生產(chǎn)過程優(yōu)化和經(jīng)營管理改善,所獲得的效益越來越小,因此開始考慮由“眼睛向內(nèi)”轉(zhuǎn)到“眼睛向外”,分析上下游企業(yè)的供需關(guān)系。到90年代,這些企業(yè)不得不把管理的視點轉(zhuǎn)移到與自己相關(guān)的、但卻是獨立的企業(yè)之間的協(xié)調(diào)和企業(yè)外部的物流、資金流和信息流的集成和優(yōu)化上。ERP盡管在90年代增加了與客戶和供應(yīng)商的交互,但仍然不具有協(xié)調(diào)多個企業(yè)間資源的觀念和能力,仍舊是面向企業(yè)內(nèi)部的事務(wù)處理系統(tǒng)。另外,ERP的計劃管理模型基本上是繼承MRP-$,存在著嚴重的弱點和不足。另外,特別是ERP缺少決策支持能力。只在事后反映企業(yè)做了什么、做得怎樣,并不能在事前告訴企業(yè)要做什么、怎樣做好。因此,發(fā)展、擴展ERP勢在必行。
高級計劃與排產(chǎn)計劃(APS)可以對總體資源和產(chǎn)品族進行長達數(shù)年的預(yù)測,可以完成ERP的主生產(chǎn)計劃、物料需求計劃、能力計劃和年度進度編制的工作。APS著眼點是整個供應(yīng)鏈,其計劃范圍已擴展到企業(yè)外部,并采用線形規(guī)劃、約束優(yōu)化、模擬、OLAP等決策技術(shù),解決許多復(fù)雜問題。因此,現(xiàn)在ERP一般同時作為APS的信息源,并接收APS計劃、決策、預(yù)測的結(jié)果?,F(xiàn)在的ERP有用APS引擎取代MRP模塊或把APS作為ERP 套件之一的趨勢,這就是擴展的ERP(ExtendedERP)概念。
從ERP提升到供應(yīng)鏈管理(SCM)和電子商務(wù)是今后的發(fā)展趨勢。目前,國外排名前50名的石化公司都普及應(yīng)用了ERP基本模塊。近90%的石油天然氣企業(yè)也都實施了具有行業(yè)特色的ERP基本模塊。
4 結(jié) 語
石油化工企業(yè)的IT投資重點是:20世紀70~80年代為DCS,90年代為ERP,進入21世紀后則轉(zhuǎn)為以供應(yīng)鏈管理為主的企業(yè)運營管理(enterprise operation management,EOM)。因為ERP回答的是已經(jīng)發(fā)生了什么,它是交易的執(zhí)行和生成歷史的報表,是現(xiàn)在看過去。EOM則回答今后應(yīng)發(fā)生什么,生成最佳決策,指導(dǎo)企業(yè)執(zhí)行最佳決策;是從供應(yīng)鏈的角度,注重增值的環(huán)節(jié),從過去、現(xiàn)在推斷、優(yōu)化將來。供應(yīng)鏈管理是一種新的商務(wù)模式和理念,它強調(diào)更多地關(guān)注價值的創(chuàng)造,而不單是降低成本;更多地關(guān)注企業(yè)組織之間和外部,而不單是組織內(nèi)部和生產(chǎn)環(huán)節(jié)。要把煉油廠、化工廠融于全球性的采購、供應(yīng)、交易、客戶的環(huán)境和國際貿(mào)易體系中。
上層的ERP、SCM、E-Business和DSS,中層的EOM 和MES,下層的DCS、PLC和ESD等的有機組合,則構(gòu)成了化工企業(yè)智能化生產(chǎn)技術(shù)的整體。
今后幾年,化工智能制造技術(shù)即化工信息化技術(shù)的重點將是檢測技術(shù)的數(shù)字化、控制技術(shù)的智能化、生產(chǎn)過程控制與經(jīng)營管理一體化,以及企業(yè)內(nèi)部與外部供應(yīng)鏈管理優(yōu)化的一體化。