Anatomy
Physically, LEDs resemble p-n junction diodes. As with p-n junctions, electrons and holes flow towards the junction when a positive differential voltage is applied between the anode (p-side), and cathode (n-side). Once an electron is recombined with a hole, it releases energy. Depending on the physical properties of the p-n junction materials, the released energy can be non-radiative, as for the typical diode applied in discrete circuits, or in the form of emissions in the optical range. For an LED, the wavelength of the emitted light (i.e., its color) depends on the band gap characteristics of its p-n junction material. Performance-wise, LED materials have relatively low reverse breakdown voltages since they have relatively low band gaps.
Colors
Red LEDs were the first to become commercially available in the late 1960s but their light output was very low. Despite this shortcoming, they were commonly used in seven-segment displays. Thanks to advancements in material science, nowadays LEDs are commercially available in a variety of colors with some of them having light outputs that would blind you if you stared directly at them.
Blue LEDs became widely available a few years ago. Mixing blue LEDs with red and green LEDs produces white light. This technique of generating white light provides a large color gamut, dynamic light tuning, and excellent color rendering (CRI), which is well suited for high-end backlighting applications. A simpler and more economical way of producing white light is to use blue LEDs and a phosphor coating that converts some of the blue light to yellow. The yellow light stimulates the red and green receptors of the eye, and therefore mixing blue and yellow gives the appearance of white. This scheme can provide good CRI but the LED's light output may suffer from inconsistent color temperatures due to manufacturing discrepancies and varying thicknesses in the phosphor coating layer.
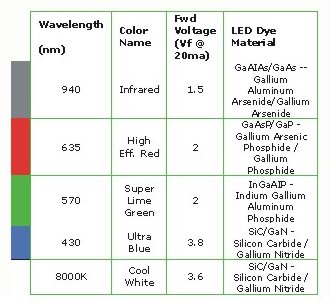
Efficiency
High efficiency is the buzz word for LED-based light sources. When it comes to lighting, efficiency is defined as the light output per unit power. Thus, in the metric system, it is measured in lumens (lm) per watt (W). Recently some LED manufactures introduced LEDs with promised efficiencies hitting the 150 lm/W mark. In comparison, incandescent comes in at 15 lm/W, and fluorescent provides 70 lm/W. So could LEDs put incandescent and fluorescent out of business any time soon? Maybe, but, unfortunately some of these LED's efficiency numbers are subject to specmanship. The problem is that LED inefficiency has to do more with the fact that a considerable portion of the produced light is reflected at the surface of the packing material back into the LED die. This reflected light is likely to be absorbed by the semiconductor material and turned into heat.
Anti-reflection coating, and minimizing the reflection angles by using a half-sphere package with the LED placed at the center, reduces the amount of reflected light and improves efficiency. However, these techniques are subject to manufacturing variations and may require high premiums to ensure consistent performance. So while LEDs are rapidly being adopted by industry, they've got a long way to go.
Applications
There are many factors which make LEDs eye-catching for high-performance modern electronics. For example, their higher light output per watt extends battery life and thus they are well suited for portable applications. In addition, an LED's fast turn-on/turn-off characteristics fit perfectly with the needs of automotive tail lights, especially the brake lights, since it improves safety by providing drivers more response time. RGB LEDs in backlighting complies with ROHS standards, since LEDs do not contain lead or mercury. LED lighting facilitates a full-spectrum light source with larger color gamut. LEDs have an exceptionally long lifespan, which enables their use in applications where long-term reliability is highly desirable, such as traffic lights. Machine vision systems require a focused, bright, and homogeneous light source—LEDs are a great match. LEDs, with their simple-to-implement dynamic light-tuning, would also allow you to set the light in your living room to green when you need to relax and to red when it's time for bullfighting.
Drivers
LEDs are inherently current-driven devices; i.e., their brightness varies with their forward current, IF. Depending on the color as well as the forward current, the LEDs' forward voltage drop, VF, varies as well. Thus, driving LEDs with a constant current is essential to achieve the desired color and brightness level. An LED driver scheme can be as simple as a voltage source and a ballast resistor (Figure 2a). This solution works best for narrow-input range, low-current applications in which the LED's forward voltage drop is slightly below the input supply voltage. But variations in the input supply voltage or the LED forward voltage drop will increase the LED current and, therefore, the light intensity and the color will shift.

Linear regulators can be used to provide tighter LED current control in small step-down ratio applications (Figure 2b). In the case of low-current step-up requirements, switching capacitor circuits can be utilized (Figure 3c).
For wide-input range, high-current applications, simple driver schemes such as those mentioned above unfortunately yield high power dissipation and poor efficiency. Consequently, more efficient and relatively more complex solutions such as switching regulators are required (Figure 2d). Switching regulators process power by interrupting the power flow and controlling the conversion duty cycle, which results in pulsating current and voltage. They can be configured in isolated and non-isolated configurations to realize voltage or current step-down (buck), step-up (boost) or both (buck-boost) functions.
In general, designers select a switching-regulator topology based on a tradeoff between cost and desired performance at a given power conversion requirement. On the other hand, in order to properly drive LEDs, the switching regulators should be configured as constant-current sources. Which switching-regulator topology can be simply configured as a current source while providing an optimal tradeoff between cost and performance? Stay tuned for part two of this series.
About the authors
Sameh Sarhan is a staff applications engineer for the Medium Voltage/High Voltage Power Management group in Santa Clara, CA. He has been involved with power electronics in various forms since 1998, having worked for FRC Corp. and Vicor Corp. His experience includes the design of hard/soft switching power supplies from a few watts to 600 watts. Sameh received a bachelor's degree in electronics engineering in 1996 from Cairo University (Egypt).
Chris Richardson is an applications engineer in the Power Management Products group, Medium and High Voltage Division. His responsibilities are divided between lab work, bench evaluation of new ICs, written work such as datasheets and applications notes, and training for field engineers and seminars. Since joining National Semiconductor in 2001, Chris has worked mainly on synchronous buck controllers and regulators. In the last three years he has focused on products for the emerging high brightness LED market in the automotive and industrial areas. Chris holds a BSEE from the Virginia Polytechnic Institute and State University.